Disc Granulator
Fertilizer Granulator Machine
Let’s Start Work
Together
Please feel free to contact us. We will get back to you with 1-2 business days. Or just call us now.
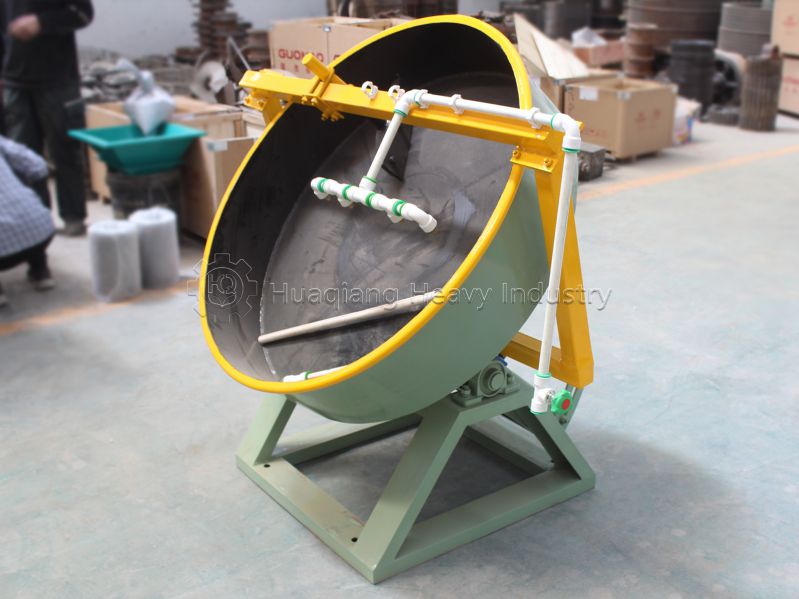
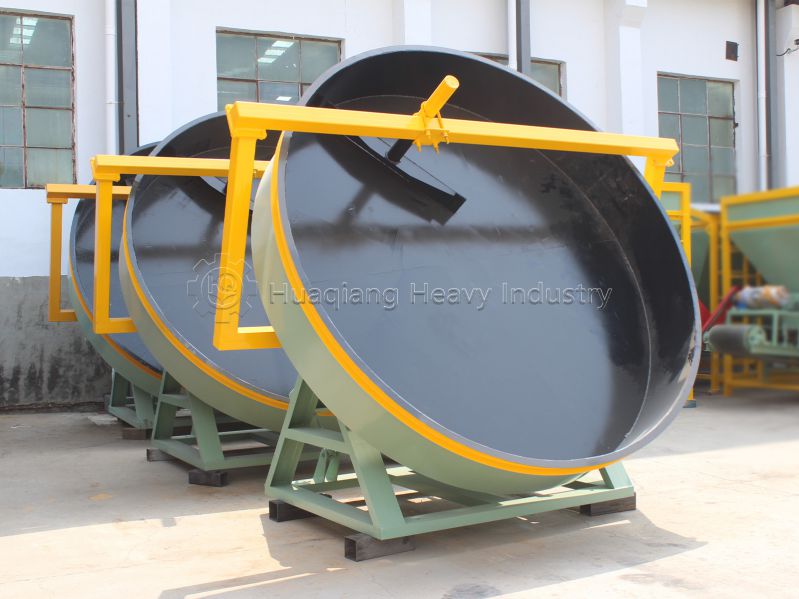
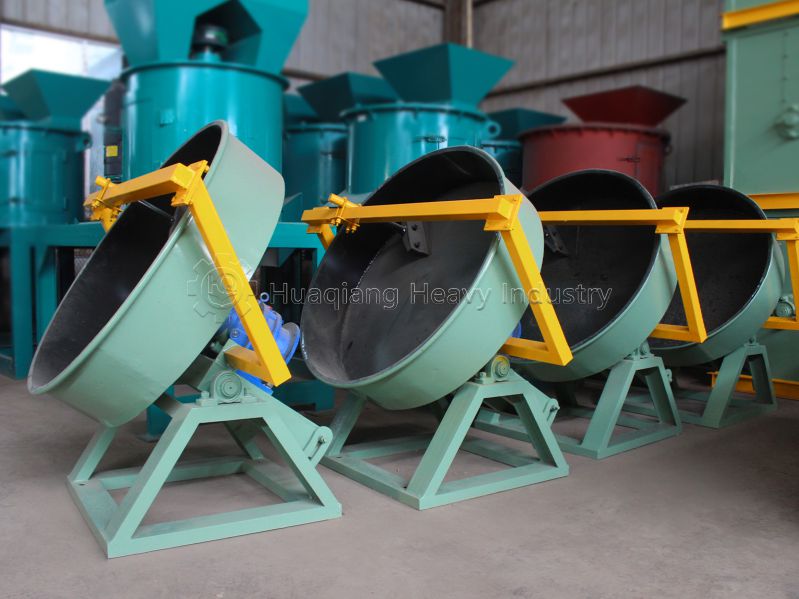
Disc Granulator
Disc granulator is a granulation equipment widely used in industries such as fertilizers, chemicals, pharmaceuticals, and food. Its main function is to form spherical particles of a certain size and shape through the centrifugal force of a rotating disk, in order to improve the flowability and performance of the material.
Scope Of Application
The disc granulator is suitable for granulating various materials, mainly including:
Fertilizer industry: compound fertilizers, organic fertilizers, slow-release fertilizers, etc.
Chemical industry: catalysts, dyes, pigments, etc.
Pharmaceutical industry: intermediates for tablets and capsules.
Food industry: food additives, seasonings, etc.
Environmental protection industry: sludge treatment, waste resource utilization, etc.
Equipment Structure And Composition
The disc granulator mainly consists of the following parts:
Disk body: The rotating disk is the core part of the granulation process and is usually made of wear-resistant materials.
Drive system: including motor, reducer, and transmission device, used to drive the rotation of the disc.
Feeding system: The material is evenly distributed to the center of the disc through the feeding port.
Spray system: used to spray liquid adhesives to promote particle formation and solidification.
Tilt adjustment device: used to adjust the tilt angle of the disc, control the movement path and granulation effect of the material.
Discharge system: located at the edge of the disc, used to discharge finished particles.
Working Principle
Material feeding: The material is fed into the center of a rotating disk through the feeding port. The feed usually needs to be uniform to ensure the stability of the granulation process and consistency in particle quality.
Centrifugal force: The rotation of the disk generates centrifugal force, pushing the material towards the edge of the disk. The magnitude of centrifugal force depends on the rotational speed of the disk and the distance from the material to the center of the disk.
Particle formation: Under the combined action of centripetal force (the force acting from the center of the disk towards the material) and centrifugal force, the material begins to roll and collide. Small particles gradually aggregate into larger particles through the adhesive force between them. This process usually requires the addition of an appropriate amount of water or binder to promote particle formation and stability.
Rolling and collision: The material continuously rolls inside the disc, colliding with the disc wall and other particles, which helps to densify the particles and circularize their shape.
Particle growth and grading: By adjusting the rotation speed and tilt angle of the disc, the size and shape of the particles can be controlled. Smaller particles continue to roll and grow inside the disc, while larger particles are pushed to the edge of the disc due to centrifugal force and discharged through the discharge port.
Discharge and collection: Particles that reach a certain size are discharged from the disc and enter the subsequent screening or cooling process to remove unqualified particles and stabilize the structure of the particles.
Equipment Features
High granulation efficiency: The disc granulator can quickly form uniform spherical particles through centrifugal force.
Easy to operate: The device structure is relatively simple, easy to operate and maintain.
Wide applicability: capable of handling various materials and suitable for various granulation needs.
Good particle shape: By adjusting the disc parameters, particles with high sphericity and uniform size can be produced.
Continuous production: The disc granulator can achieve continuous material feeding and particle output, suitable for large-scale production.
Moderate energy consumption: Compared to other granulation methods, the energy consumption of the disc granulator is relatively low, and the operating cost is moderate.
High flexibility: By adjusting the disc speed, tilt angle, and spray system, the size and shape of particles can be flexibly controlled.