Rotary Drum Granulator
Fertilizer Granulator Machine
Let’s Start Work
Together
Please feel free to contact us. We will get back to you with 1-2 business days. Or just call us now.
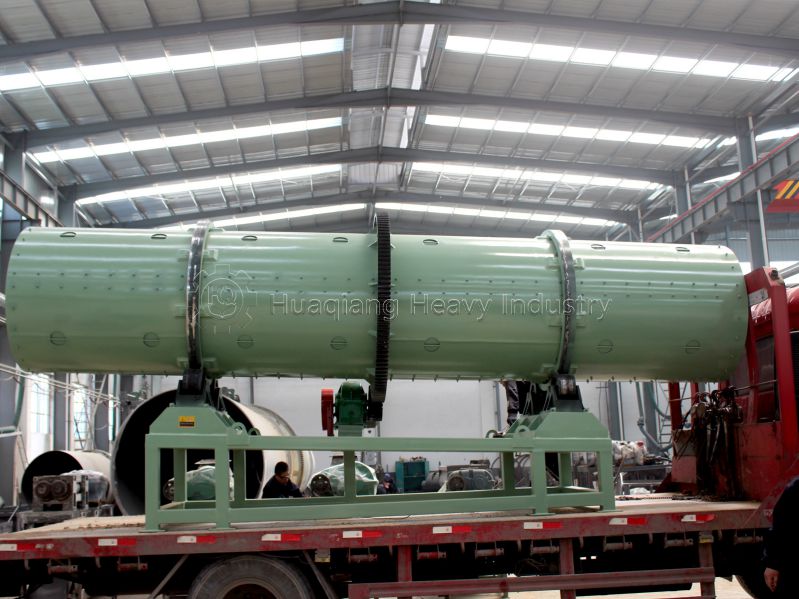
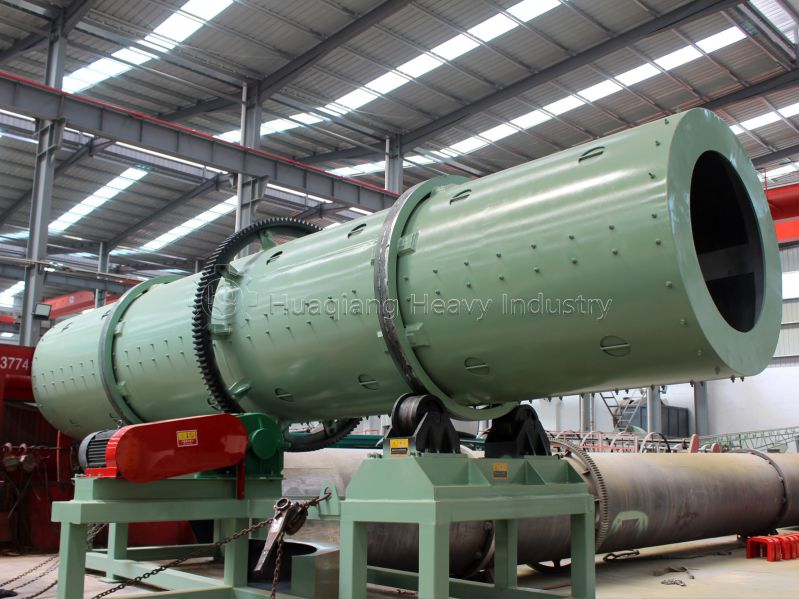
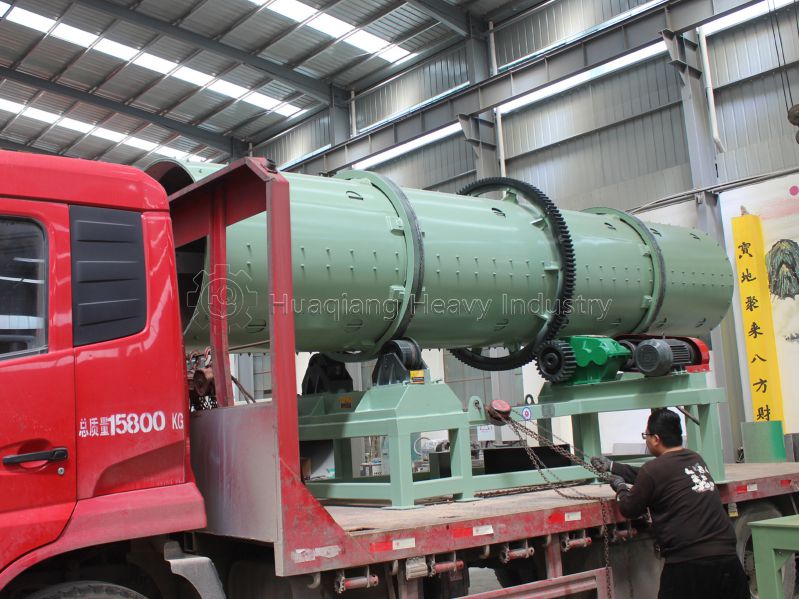
Rotary Drum Granulator
A rotary drum granulator is a device that forms particles under suitable humidity conditions by rolling and colliding materials inside a rotating drum, utilizing the viscosity of the materials themselves and external binders. This granulation method is widely used in industries such as fertilizers, chemicals, food, pharmaceuticals, etc., and is particularly suitable for processing powdered or fine-grained materials.
Scope Of Application
The rotary drum granulator is suitable for granulating various materials, including but not limited to:
Fertilizer: Produce various types of fertilizers, such as compound fertilizers, organic fertilizers, biological fertilizers, etc.
Chemical products: Production of chemical raw materials such as catalysts, adsorbents, desiccants, etc.
Food processing: such as producing instant powder, seasoning granules, etc.
Pharmaceutical industry: preparation of medicinal granules, tablet raw materials, etc.
Equipment Structure And Composition
The rotary drum granulator mainly consists of the following parts:
Rotating drum body: made of rolled steel plates, with lifting plates or spiral blades on the inner wall to increase material rolling and collision, and promote particle formation.
Transmission device: including motor, reducer, and transmission sprocket, providing power for the rotating drum body.
Supporting device: It supports the weight and rotation of the drum body, usually using rolling bearings or sliding bearings.
Spray system: It is used to spray proper amount of water or binder during granulation to control the humidity and viscosity of materials.
Feeding and discharging devices: including feeding and discharging ports, used for the entry and exit of materials.
Control system: used to monitor and adjust the operating parameters of equipment, such as speed, humidity, temperature, etc., to ensure the stability and particle quality of the granulation process.
Working Principle
Material pretreatment: Before entering the drum, materials usually need to be pretreated, such as crushing and mixing, to ensure the uniformity and appropriate particle size of the materials. Meanwhile, as needed, the material may need to adjust its humidity to increase its viscosity and facilitate granulation.
Material feeding: The preprocessed material is evenly fed into the rotating drum through the feeding port. At this point, a certain level of humidity may have been pre-set inside the drum or adhesive may have been sprayed to promote particle formation.
Rolling and collision: Within the drum body, the material is driven by the rotation of the drum body. As the drum body tilts and rotates, the material rolls and collides within the drum body, forming small aggregates. This process promotes the adhesion between materials, gradually forming particles.
Particle growth: Small aggregates continuously adsorb surrounding fine powder during rolling and collision processes, gradually increasing and forming particles with a certain size and strength. By controlling the rotational speed, tilt angle, and material humidity of the drum, the growth rate and final size of particles can be influenced.
Spray humidification: during the granulation process, it may be necessary to spray appropriate amount of water or binder into the drum body through the spray system to maintain the appropriate humidity of materials and promote the formation and growth of particles.
Particle maturity and discharge: When the particles reach the expected size and strength, the mature particles are discharged from the discharge port by adjusting the speed and tilt angle of the drum, and then enter the subsequent cooling, screening, or packaging processes.
Equipment Features
Strong adaptability: Suitable for materials of various properties, able to handle a wide range of particle sizes and humidity.
Good granulation effect: uniform and dense particles can be produced by adjusting the rotating speed, tilt angle and spray amount of the drum.
Continuous production: capable of achieving continuous material feed and particle output, with high production efficiency.
Flexible operation: By changing the process parameters, the size, shape, and strength of the particles can be adjusted.
Stable structure: The drum granulator has a stable structure, runs smoothly, and is easy to maintain.
Moderate energy consumption: Compared to other granulation methods, the drum granulator has lower energy consumption and minimal environmental impact.